What are the shocks that Electric Hoist is vulnerable to?
The Electric Hoist structure is generally very compact. The electric hoist whose motor axis is perpendicular to the drum axis generally uses a worm gear drive. Its shortcomings are large length, large width, rough structure,
low mechanical efficiency, and difficult processing.
The hydraulic system is generally dual-controlled, and both the overflow regulating valve and the magnetic contact pressure gauge can accurately control the pressure. The electrical control department adopts low voltage control, which increases the safety of the control system. Through field observation, Electric Hoist will be affected by various vibrations during use:
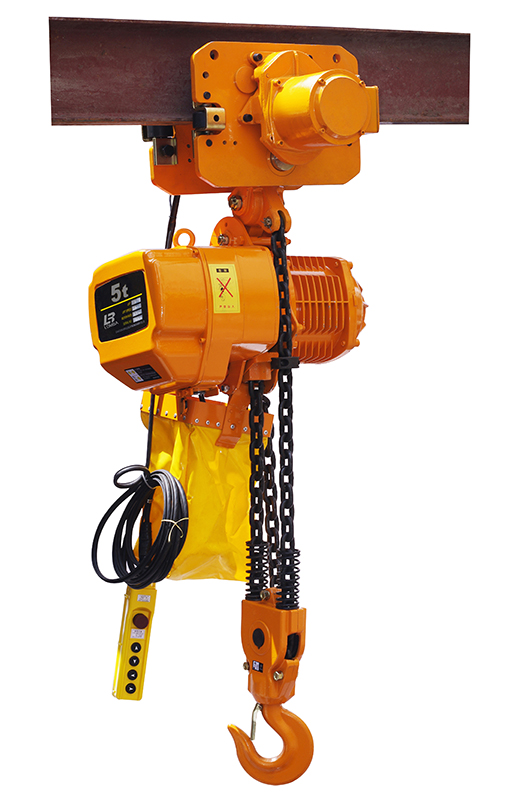
2. Vibration caused by starting and generating of walking and lifting motors;
3. The vibration generated by the vibrator of the acetylene generator is transmitted to Electric Hoist through the hopper and steel cable.
4. Vibration generated when the internal contactor of the control box is closed and released.
5. The bottom plate is fixed with M6 screws without spring pads. Only 3 of the 4 screws should be installed, and the screw holes are not completely aligned during processing.
It should be said that the vibration from all aspects of Electric Hoist is the external cause of the internal wire loosening and disconnection of the control box, and the defects in the design, processing and installation are the internal reasons.